Arjo Care Covid-19 Report: Canada
The Covid-19 pandemic has put our customers in healthcare around the globe – and the field service teams who support them – in extraordinary situations.
From Canada, we talked to field service technicians Derryk Wilson, Roger Liu, Jarret Chessell, Pat Reardon, Steve Grein and Trevor James, all of whom drew from past experiences to stay safe and support our customers “outside the box”.
An unprecedented crisis
In his 32 years with Arjo, senior field service technician Derryk Wilson has never experienced anything like the Covid-19 pandemic.
“There was SARS in the early 2000s, which was terrible in eastern Canada, but in western Canada where I’m based, it didn’t affect my day at all,” Derryk explained. “It seems it was less transmissible. Covid-19 is far more transmissible; people can walk around asymptomatic.”
Steve Grein, who has been with Arjo since 1995, was in eastern Canada when SARS hit.
“SARS didn’t last very long here. Maybe three or four months and then it was kind of back to normal again,” Steve recalled. “This (Covid-19) has been quite long.”
When Covid-19 first hit Canada, our technicians’ biggest adjustment was dealing with the dip in workload.
“From March until the summer of last year, it was very slow. One of the guys working alongside me retired, so I had to cover both our territories. Normally I would do this when he went on vacation, and would be almost overwhelmed within two weeks. But now even though I was doing it for 9 months, it was not that much different from having my own territory, it slowed down that much,” explained Steve. “Nobody was calling because nobody wanted anyone in their facility unless it was absolutely necessary.”
While low traffic is usually a sign of quiet times, in reality our customers were dealing with an unprecedented crisis.
“When it first hit, our customers felt stressed, overworked, fearful, anxious… there were a lot of unknowns,” recalled Trevor James, who joined Arjo in 2003. “Their biggest fear was that they would get infected and sick, or bring it home to their families. Some of their peers were dying from it.”
“To make it worse, this meant a shortage of staff. There was lots more overtime due to the rise in patient numbers, more time spent taking safety precautions, constant changes… it was a perfect storm,” Trevor added.
“There was immediate panic at the beginning, and nobody knew what to do at first,” said Derryk. “The health authorities hadn’t made any decisions or provided any guidance yet, so care facilities just did not want us to come in unless it was an absolute dire emergency.”
In some cases, the lag in workload had to be self-imposed.
“I travel back and forth between provinces. That’s been challenging as each province has their own guidelines and requirements,” explained Pat Reardon, who has served two decades with Arjo and is based in the coastal Maritime provinces. “Right now one of my provinces is in an outbreak. Some customers want me to visit but if I go there, then I won’t be able to come back into my own province – no one will want me inside their building because I’ve been to an area in outbreak.”
“We've had to reschedule a lot more often than before,” said Roger Liu, who is counting his third year with Arjo but has been servicing healthcare equipment since 2003. “Before the pandemic I’d start my day by checking my call board and making arrangements for the day or for the week. During the pandemic, I first check the regional health authority website to find out which places have had an outbreak. If there’s an outbreak we cannot go to those facilities.”
“Even before Covid-19, if there was any sort of outbreak at a care facility, they will ask me not to come, and we would just try to reschedule,” said Jarret Chessell, who joined Arjo in 2017. “But I’ve been able to reschedule and visit every customer on my roster so far. We do what we can to help our customers keep everything running smoothly and they saw the value in that.”
Service from a distance
Although restricted from physically visiting care facilities, our technicians soon found ways to support our customers from afar.
“When I first started with Arjo 30 years ago, I was the only technician in the country – the first they ever hired in Canada,” said Derryk. “I could be in one province and find out there was a service request two provinces away, and it would take me two days to drive there. If I can’t get to a facility quickly enough, then they might choose to take on repairs themselves with guidance from me over the phone.”
“Sometimes I had to do this at a payphone, outside, in Canadian winter,” Derryk added with a chuckle. “There was no video calling back then, no Facetime. The height of technology was a fax machine.
“The truth is there is no typical day for us. Every day is different. You never know what time you’re going to be away, and exactly what time you’re going to be home, or what you’ll find when you get to the care facility. Very often things are not as they were communicated to you. You have to be ready to pivot and roll with whatever changes you’re presented with.”
“In service, you’re never going to say no I’m not coming, there is no solution. I will always try to come up with a solution," said Roger. "So I started suggesting that they push this lift into the parking lot and I will service it there. That way we’re both good – you got your equipment serviced, and I didn’t enter your facility.”
“If the equipment was mobile, we would bring them outside, or move it to a basement, loading area, or parking lot – far removed from patients and residents,” explained Trevor. “I would wipe everything down and service the equipment, then disinfect myself and change out of my gear. Then someone would come and collect the equipment.”
“Some equipment can’t be moved, like bathtubs. So if they have an in-house technician, customers would offer to fix it themselves while we guide them over the phone, and we would ship them the parts they needed,” said Steve. “But more often they ended up waiting two or three weeks until they were out of outbreak, then called me to come back and repair it.”
“We’re not easily stressed.”
The nature of their work has also prepared our technicians to deal with periods of isolation.
“When I worked as a technician in China, I covered four provinces, which is a huge area. I used to spend three weeks away, then one week at home, or leave on Monday morning and not be home until Friday night, travelling across the four provinces,” Roger recalled. “This was back in the early 2000s, when we still didn’t have the high speed train, and some places didn’t have airports. To reach a customer I’ve had to drive, or take a bus, sometimes a tractor, and I have even had to ride a rickshaw pulled by cattle!”
“Both before and during the pandemic, we spend a lot of time alone on the road. We work in different areas and provinces, and we’re spread out across the country, so most of us don’t live or work close to each other and rarely get face-to-face contact with our co-workers,” said Pat. “We’re Maritimers. We’re not easily stressed. We take it one day at a time, and go with the flow.”
“The ones running the care facilities may have been a little more stressed. But their staff are still reporting in for work. If they have to wear a mask, we’ll wear a mask. We all have a job to do,” Pat added.
Despite their resourcefulness and resilience, there was one issue our Canadian technicians simply could not resolve on their own.
“The only customer stress I’ve encountered was due to global shortages in parts. This was a global problem and not just an Arjo problem,” said Derryk. “I have one customer who ordered 10 parts in January. The projection is that they will only get them in June, and that’s the fourth or fifth time this shipment has been delayed. If we don’t get the parts, we just can’t fix the equipment.”
“There’s a replacement part I’ve been waiting on for three months, but the customer has been waiting for six months,” revealed Pat. “I actually received the part months ago but at the time they were in outbreak and would be for a while, so I used the part somewhere else that also needed it urgently, and re-ordered it. We didn’t expect to have to wait so long for the next part to come in. So they’ve had a tub that’s been down since November last year because of parts delays and Covid-19.”
All the technicians agreed that communication was crucial for maintaining a positive relationship with customers through such challenges.
“The key is to stay in touch,” said Derryk. “As soon as I get an update on a delay, the first thing I do is call the customer to let them know. And I recognised that it was not the news we wanted to hear, but at least they were getting immediate updates.”
“I feel that [the customers] are all very happy. I think they’re very satisfied. All of us have gone out of our way to try and help them out even when we’re not allowed to visit them,” said Jarret. “Probably we’ve communicated with customers even more in the past year because if we’re not allowed in a facility, we have to work together to try and come up with a resolution. And I’d say they were very positive and they appreciate us doing that for them.”
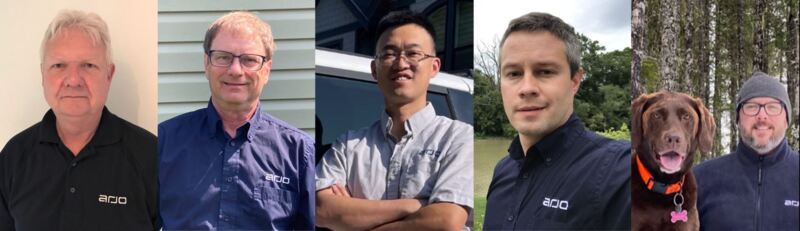
Pictured from left to right: Steve Grein, Pat Reardon, Roger Liu, Jarret Chessell, and Derryk Wilson with an enviable isolation buddy.
Back onsite – with safety precautions
As the pandemic wore on, service technicians were allowed into care facilities again, albeit with a laundry list of safety precautions.
“The pandemic has increased significantly the time I spent responding to a service call,” said Trevor, who covers the downtown Toronto area. “When I arrive at a facility, there is a screening process that takes around 15 to 30 minutes. Then we have to wear PPE gear, a mask and a face shield, which is necessary for protecting myself and others, but a face shield fogs up when I breathe, so this impairs my vision and slows me down while I work. Some types of PPE are more durable than others, especially in the beginning when there was a shortage. As soon as you put it on you can feel the quality. We’d feel it tearing as we moved or bent over to inspect the equipment. And just imagine – caregivers have to wear that for a full shift.”
“Every service call that I go to, I do the rapid test, and sometimes I need to do it again before I can be admitted into the next facility,” added Trevor. “Some days I have to be tested three to four times a day. Some facilities require a negative test no more than seven days old. Sometimes it takes a few days and because of the lag in getting test results, I have to keep getting a new test.”
|
Trevor James (right) and colleague Shyam Mahedeo don full protective gear during a customer site visit. |
“In the first month, there was a shortage of protective gear and there were no set rules,” recalled Steve. “Then the screening came in, then the masks, then the gowns. They didn’t all come in at once. One facility would do it one way, and another facility would do it another way. So I’ll go to one place and wear a mask, then the next place will want me to put a gown on and goggles.”
Aside from various protective gear, the technicians were no strangers to strict infection control routines, having been conscious of infection risks even before Covid-19.
“I’ve been very diligent about hand washing for my entire career. It’s very rare for me to get ill, and when I do it’s always mild,” revealed Derryk. “During flu season I would always get a flu shot, because I never want to be the person responsible for carrying a bug from facility to facility. It’s not mandatory, but I take my own initiative.”
“I get a flu shot too in flu season, because we enter a lot of senior homes and there are vulnerable residents in there,” said Roger. “It just makes sense to me so I won’t carry a virus into a facility.”
“I’ve always washed my hands constantly, and I’ll continue to do that,” said Steve. “I’ve got a bottle of hand sanitizer in the van.”
“I call it a work self-isolation program: Go to work, go home, don’t go to restaurants, don’t go to supermarkets or grocery stores, as much as possible,” said Pat. “I eat in my car, and don’t go into restaurants for lunch. Like Steve, I wash my hands and keep a bottle of hand sanitizer in the car.”
All these precautions seem to have paid off: None of the interviewed technicians say they have experienced any symptoms to date. Among 68 service staff including 62 field technicians in Canada, only one team member has tested positive for Covid-19 during the entire pandemic season.
While thankful for their own good health, some loved ones were sadly lost to the deadly virus.
“My brother and sister-in-law, who are based in Virginia and work in Washington DC, both passed away from Covid-19. I had an elderly aunt in a nursing home who caught it from her roommate and passed away over Christmas. And so did my wife’s uncle,” revealed Trevor. “So we had four funeral services over the Christmas holidays, which we had to attend virtually.”
“We have plans to hold in-person memorial services after things calm down, but that might be a long way off, especially if we have to travel across the border. Sometimes I still hear people tell me the virus is a hoax... I’m not angry. I just wish they were better informed. I wish they could follow me on a day of work and see what I’ve seen. Then they won’t think it was a hoax anymore.”
Looking forward to normalcy
What lessons are our technicians taking from the pandemic experience?
“I think it has helped to shine a brighter light on what we do, particularly the use of the word essential, because what we do is critical to the care of the residents we serve,” said Derryk.
“Our job is so important, which you especially feel during this pandemic, because sometimes we can’t repair the equipment on time, or the facility can no longer share their equipment between different wings,” said Roger. “And when it is no longer accessible, it’s a painful reminder just how essential that equipment is for their residents. I keep learning how important my work is to support people.”
As things slowly return to normal, what do they look forward to the most?
“In early 2020 I gained some new customers on my roster,” said Steve. “There’s one facility that I have been visiting once a week for over a year now, and I have yet to meet anybody. It’s all arranged through email. I go there, check in, do the work, and check out. I’m looking forward to the time where I can see people face to face again.”
“I used to just pop in on people and see if they need any help,” said Jarret. “But now you need to get on the phone, contact them ahead of time and make sure it’s okay. Because you don’t want to drive 2 hours somewhere and find out you can’t go in.”
“I want to stop eating in my car,” said Pat. “I’d rather go inside and eat.”
Find out more about Arjo Care here or read more Covid-19 stories from USA, Spain, and the Netherlands on the Arjo Blog.